Bonjour,
Étant pensionné depuis à peine deux mois, Bernard Canet m’avait sollicité pour rédiger un article sur les BB 27000/27300/37000/37500. Celui-ci a été publié dans VF 155 de mai-juin 2006. Il n’est donc pas question de le recopier intégralement, ni même partiellement. Il vaut surement mieux s’intéresser à la manière dont le projet a été vécu, notamment par les services techniques de la SNCF, et en particulier pour la partie caisse qui m’était dévolue.
Auparavant, lorsque la SNCF lançait un appel d’offres pour du matériel roulant, elle rédigeait un cahier des charges volumineux dans lequel les solutions techniques, telles qu’elle voulait les voir appliquées, étaient presque intégralement décrites dont certaines étaient même dessinées et jointes en annexes. Par exemple, le cahier des charges du TGV PSE comportait quelques 900 pages avec les annexes ! Pour les BB 27000, c’est une révolution (tant pour la SNCF que pour le(s) constructeur(s) d’ailleurs) puisque l’appel d’offres s’est fait sur la base d’un cahier des charges fonctionnel (cdcf) dans lequel on se contente de définir les grandes lignes du produit, ses capacités, les performances et la disponibilité que l’on attend de lui. Il comporte néanmoins plusieurs dizaines de pages ! Dans le cas de la BB 27000, désignée « locomotive Fret » à l’origine du projet, le soumissionnaire doit remettre une offre chiffrée en termes de coûts d’acquisition et de possession, une offre technique, un plan d’homologation, un plan de justification de la définition, une trame de maintenance et un prototype. Une fois reçus par le client, ces documents sont ventilés dans les services compétents pour notation de l’offre et, bien évidemment, les notateurs techniques ne sont pas informés de l’offre financière afin de ne pas influencer leurs jugements. Reste ensuite au client de retenir le « mieux ou le moins disant », à sa guise… Quand j’ai pris mon poste aux caisses locomotives, toutes ces étapes avaient déjà été franchies : le constructeur retenu était Alstom et ce dernier était en cours de réalisation de sa Prima 1. À partir de cet instant, les documents contractuels sont devenus « mes livres de chevet (professionnels) ».
Les équipes, tant coté client que fournisseur, sont constituées de manière assez symétrique et comprennent : un Chef de projet, son adjoint et le secrétaire, un représentant juridique et un responsable de lot dans chaque domaine technique (bogie-captage, caisse, frein, électrique). L’équipe SNCF comprenait en outre deux électriciens (l’un pour la chaine de traction, l’autre pour l’informatique), trois représentants de la maintenance dont deux étaient attachés aux ateliers d’Oullins (désigné atelier directeur de la série) et un du dépôt d’Avignon (établissement où les BB 27000 ont été mises en service) et, enfin, un représentant du contrôle en usine. Ces équipes sont réunies toutes les six semaines lors de réunions plénières (RP). Les responsables de lots doivent informer le secrétaire SNCF des sujets qu’il souhaitent aborder en RP une dizaine de jours à l’avance afin qu’il les transmette à son homologue de chez le constructeur, ce dernier adressant aux participants l’ordre du jour complet, une semaine avant la date retenue lors de la précédente RP.
Chaque responsable de lot se repose sur des experts dans les spécialités dont il a la responsabilité : en ce qui me concerne, pour assurer ma mission, je m’appuyais sur les experts dans les domaines des ossatures de caisse et de la sécurité passive, la climatisation, la lutte contre l’incendie, les aménagements et revêtements intérieurs, les peintures, le gabarit, les vitrages, la production d’air comprimé, les essuie-vitres, etc. La caisse est une ossature à part entière mais elle repose sur des bogies et recèle tous les équipements intérieurs et extérieurs dont il faut aussi gérer les interfaces.
Au fur et à mesure de l’avancement du projet, le constructeur édite des documents qu’il transmet au client via le secrétaire de projet, qui les enregistre dans une base de données et les ventile au responsable de lot concerné. Lorsqu’un organe, un produit ou un ensemble est défini par le constructeur, il fait l’objet d’une spécification technique et de dessins de détails ou d’ensemble. Ces documents doivent être analysés par le responsable de lot et il doit aussi les transmettre à ses experts et aux représentants de la maintenance. Tous ont accès à la base de données pour transcrire les commentaires éventuels, mais seul le responsable de lot a le pouvoir (et le devoir) d’attribuer la note suivante, dont le représentant du contrôle en usine est aussi informé :
- « A » pour approuvé (tout va bien).
- « OT » pour observation technique, ce qui signifie que l’on est d’accord sur le fond mais pas forcément sur la forme et que la recherche d’une correction commune sera recherchée. Ce n’est pas une entrave à la poursuite du projet.
- « OM » pour observation majeure : contractuellement, c’est l’arrêt immédiat de la fabrication, mais dans les faits la construction continue…
Lorsqu’il y a un tel désaccord, les acteurs du projet instaurent une réunion technique spécialisée (RTS) au cours de laquelle on ne traite que du sujet litigieux, entre experts, évitant ainsi de polluer les RP. Le constructeur peut aussi initier une RTS par laquelle il veut faire part d’évolutions techniques nécessitant l’accord du client : pour ma partie, il y en a eu une bonne dizaine. Il m’est arrivé à plusieurs reprises d’attribuer l’OM et, dans pratiquement tous les cas, de lever la sanction dès lors qu’ un accord avait été trouvé en RTS. La seule observation OM qui est restée en l’état a concerné le test de résistance de la structure de caisse de la BB 37001 : j’étais vraiment fâché contre le constructeur, ayant le sentiment qu’il aurait pu faire mieux et pas plus cher, pour cette caisse de locomotive notamment pour les tôlages de face. Lors d’une rencontre avec d’anciens collègues, j’ai appris que la sanction n’avait été levée que bien après la livraison de la dernière machine électrique de la gamme Prima, soit bien après ma retraite.
Dans ma partie, les points les plus forts autour de cette BB 27000 ont été :
- redéfinition de la cloison de séparation entre la cabine et le compartiment moteur. Cette cloison comporte une porte qui donne accès au compartiment arrière mais qui est également, et c’est bien-là le fondamental, l’issue de secours du conducteur. Sur la Prima 1, le linteau était situé à 1710 mm du niveau du plancher, à tel point que les techniciens d’essais avaient disposé des mousses les protégeant des chocs à la tête. Lorsque j’ai appris que les 27000 auraient la même disposition, j’en entamé ma première croisade ! La fiche UIC 651 disait : le couloir d’évacuation (dont la porte y donnant accès fait partie) mesure 1800 m de haut sur 450 mm de large et doit garantir un passage minimal défini par un rectangle vertical de 1710 x 400 mm. Autrement dit, on peut accepter un pan coupé dans la hauteur, voire un seuil inférieur à franchir. Je ne sais pas combien de courriers j’ai pu rédiger sans faire bouger l’adjoint au chef de projet, un peu trop « psychorigide » à mon gout. Finalement, après trois mois de lutte, le Directeur de l’usine de Belfort a tranché : les tympans des cloisons des deux premières locomotives ont été modifiés à une hauteur de 1870 mm et les locomotives suivantes en ont bénéficié de série. Après coup, le Chef du département des locomotives, qui était aussi le Chef de projet, avait remercié mon opiniâtreté par courrier adressé à mon supérieur hiérarchique, mais m’avait verbalement déclaré : « au début de cette affaire de porte, je me suis demandé si tu n’étais pas un peu emmerdeur. Mais finalement, j’ai conscience que grâce à toi, nous avons une locomotive aux critères actuels et surtout que, sans ton insistance, nous n’aurions jamais pu l’homologuer ».
- redéfinition de la traverse fusible monobloc d’origine : cette traverse présentait plusieurs inconvénients dont sa masse, son coût d’usinage et la « programmation de sa déformation » qui était loin d’être certaine. Par contre, la nouvelle conception en trois éléments séparés (deux modules latéraux d’absorption d’énergie et un module central pour le dispositif de traction) a permis d’éliminer les inconvénients de la précédente.
- remplacement des essuie-vitres d’origine à deux bras et à motorisation électrique par un essuie-vitre mono bras et à motorisation pneumatique (dérivé de l’essuie-vitre du TMST). Le dispositif d’origine devenait inefficace dès 80 km/h et ne répondait pas aux critères requis.
D’autres points ont été modifiés, d’importance moindre, mais tout aussi utile :
- amélioration des ventelles des lanterneaux de sortie d’air en toiture.
- amélioration de la climatisation de la cabine.
- doublement des conduites CP/CG et élargissement des plateaux de tampons à cause des grands porte-à-faux.
- amélioration du siège du conducteur.
- amélioration de l’étanchéité des capots de toiture.
- simplification du montage des lests.
- abandon du fraisage de la traverse de tête avant soudage au châssis !
Et la liste est encore bien longue, je dirais une bonne vingtaine de points supplémentaires.
Puis, Alstom avait lancé une première vague de modifications visant à dégager des économies sur la construction de la machine. Nous avions participé à une réunion de type « brainstorming » à ce sujet sur deux jours dans un cadre verdoyant. Quelques temps plus tard, nous avions à nouveau été réunis pour une vaste opération de « redesign » de la loco. Si l’on compte tout cela mis bout à bout, j’estime à plus de cent modifications caisse entreprises depuis l’origine du projet. On peut donc se poser la question : le constructeur était-il suffisamment armé pour étudier seul une locomotive, sans l’apport des compétences de la SNCF ? Je crois que pour une première réalisation répondant à un cdcf, la réponse est non ; de même que je suis convaincu qu’après le retour d’expérience des locos de la gamme Prima, la réponse serait aujourd’hui assurément oui. Je prends pour exemple la façon remarquable avec laquelle Alstom a étudié son AGV : dommage qu’il n’ait pas trouvé plus d’acquéreurs. Et que dire de la maintenance, Alstom était à l’époque bien incapable d’en écrire une seule ligne.
En tout cas, c’est un projet qui m’a captivé durant les quatre années que j’ai passées aux locomotives. J’ai été intransigeant (dans le respect de la bienséance et du soutien de ma hiérarchie) dans la défense de l’intérêt de mon Entreprise, notamment lorsque le produit ne répondait pas aux spécifications du cahier des charges, aux normes en vigueur ou aux règles de sécurité. Par contre, dès lors que le constructeur proposait une solution GAMÉ (globalement au moins équivalent) pour réduire ses coûts de production, j’ai toujours été à son écoute. Dans la mesure du possible, lorsqu’une solution lui permettait de dégager des économies, je négociais la fourniture des pièces nouvelles à titre gratuit et la SNCF prenait leur montage à sa charge : du rétrofit à moindre coût. De plus, ça ne coûtait pas grand-chose de contribuer à la mise à disposition les installations SNCF pour faciliter la tâche de leur SAV. De bons compromis finissent toujours par coûter moins cher que des situations conflictuelles lancinantes.
Il n’y a qu’un sujet qui m’a laissé un gout amer pour ne pas avoir réussi à le faire changer : c’est la barre de liaison caisse bogie, dite de traction-compression. Cette barre pèse 230 kg, elle est taillée et usinée dans de la tôle de 130 mm d’épaisseur dont je n’imagine même pas le coût de fabrication. Pour « tomber » un bogie, sa dépose est complexe et nécessite une table élévatrice spécifique. De plus à l’origine, elle était responsable d’ondes vibratoires longitudinales de la caisse et générait une fréquence parasite dans les moteurs de traction. Ceci a momentanément été résolu par l’assouplissement des rotules caoutchouc dans les têtes, en espérant que le vieillissement du caoutchouc n’aura pas de fâcheuses répercussions. Enfin, cette barre occasionne un déséquilibre de 500 kg entre les deux essieux d’un même bogie, valeur qui passe à 1000 kg sous charge, les pesées des locomotives l’attestent. Alstom disait ne pas vouloir la changer afin d’éviter une nouvelle homologation du bogie, alors qu’on aurait pu se contenter de tester uniquement les traverses extrêmes sur lesquelles on aurait disposé les nouvelles attaches, à mon avis la SNCF l’aurait accepté. Je prônais une liaison caisse-bogie du type CC 6500 qui est d’une simplicité notoire et qui a donné entière satisfaction. Cette affaire avait occasionné une réunion au 15 rue Traversière en présence du Directeur Général d’Alstom Transport et de tous ses collaborateurs dans le projet BB 27000/37000, face à tous leurs homologues de la SNCF. À la fin de la réunion, Roland Bonnepart, Directeur du Matériel SNCF, a déclaré : « je note que nous avons fini par accepter une position commune pour maintenir cette barre de liaison, mais je vous demande aussi de noter qu’il y en a un qui n’est pas d’accord ; c’est Mr. Bayle ». Ce qui me laisse à penser que la BB 27000 (et ses cousines) est une bonne machine ; il s’en fallait de peu pour qu’elle fut une très bonne machine.
Le Chef de projet Alstom était Philippe Colignon, auquel Jean-Jacques Lang avait succédé : je l’avais précédemment connu en qualité de Chef de projet BB 36000. Récemment pour l’article de Ferrovissime, j’ai contacté Jean-Jacques Lang par mail. Dans la demi-journée qui a suivi, il m’adressait les images pour lesquelles je l’avais sollicité, avec un mot d’accompagnement très courtois, ce qui me semble bien traduire la qualité des relations que nous avons entretenues durant un projet difficile pour nos deux Sociétés. Dix ans après, rien ne l’y obligeait : s’il me lit, je l’en remercie publiquement.
Vues extérieures de la BB 27000.
Coupes transversales et horizontale de la BB 27000.
Face avant de la BB 27000. Ces trois dessins d’ensemble datent du tout début du projet et non pas été mis à jour dans les moindres des détails.

- Le pupitre en position centrale. (photo Alstom)
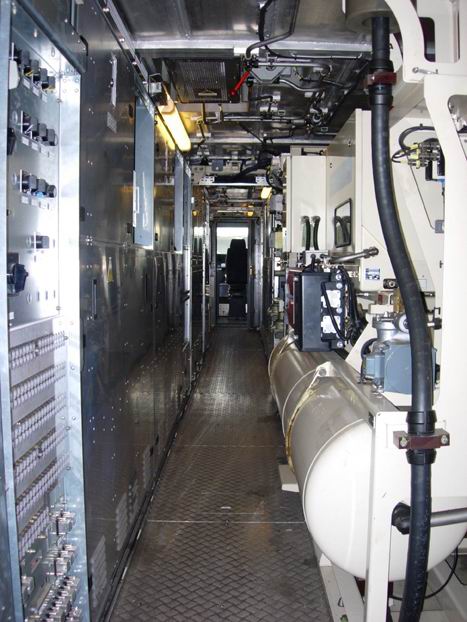
- Vue intérieure du couloir : à gauche l’armoire système suivie du bloc moteur 1, à droite l’unité de production d’air et les réservoirs principaux. (photo Alstom)
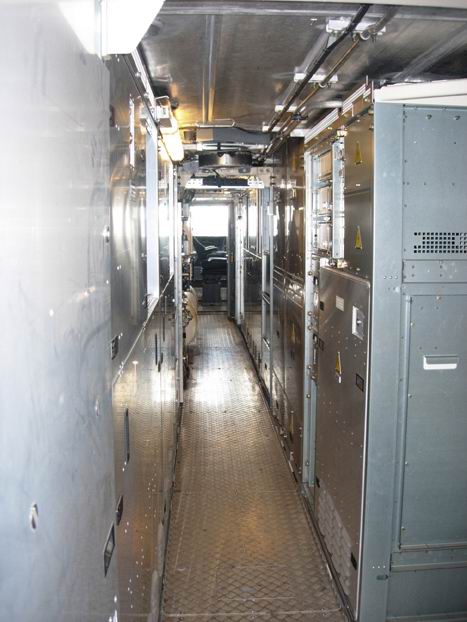
- Vue intérieure du couloir : à gauche le bloc moteur 2, à droite le bloc commun suivi du bloc rhéostatique. (photo Alstom)
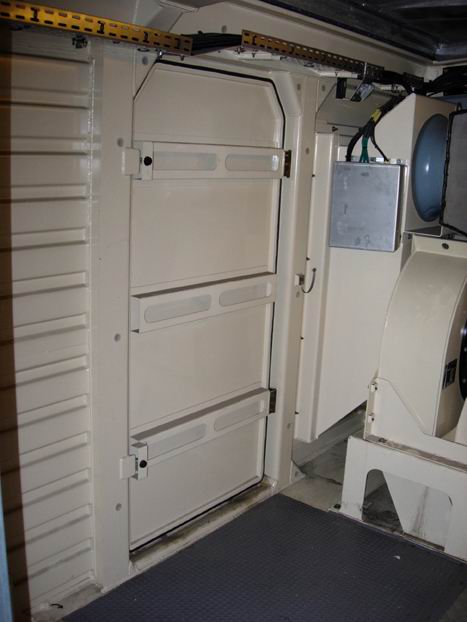
- Vue intérieure de la trappe de maintenance. (photo Alstom)
Sous cet angle, je ne la trouve pas si moche que ça ! En élévation, elle craint plus…Si mes souvenirs sont bons, c’était lors de JPO au dépôt de Lens.
Deux machines sur lesquelles j’ai bossé. La rouge est quand même plus chouette que la verte.
La BB 27124 à Juvisy en mars 2014. J’avais cru comprendre que Fret SNCF n’était pas bon (entre autre) à cause de la faible productivité de ses locomotives. Cette machine est restée sur place durant une semaine ; sur les cotés, il est inscrit « ETF recrute www.etf.fr ». Alors, je me suis dit, ça fait quand même un peu cher comme panneau publicitaire, à moins que l’on soit en attente de recrutement pour la faire bouger. Pardonnez-moi, j’ai très mauvais esprit…
2B.